9-Step VSM Simulation. (Value Stream Map)
This 9-step simulation event focuses on the point processes in the value chain from customer order to customer delivery, one process at a time.
This presentation event is part of the Deluxe-Plus VSM Lean Factory Simulation Package, or the VSM Upgrade Kit can be obtained as an optional purchase for use with the standard Deluxe Car Factory Kit or any of the other Deluxe-Plus Car Factory Kits. It is included in the Grand Package.
The event uses two Car Factory material kits, laminated participant instruction placemats, laminated control cards (material requisition, non conforming material, job ticket and heijunka cards, and six visual control flags.)
Once the team is familiar with the point process flow simulations as detailed in the simulations like Learning to See the Waste or the TPS simulation, they are ready to really look at the tools of lean and learn to use them to improve the entire value stream. Here the people see that just making any single point process, like assembly, be the best it can be may still result in no net difference to the financial bottom line.
The VSM simulation shows the chain is only as strong as it's weakest link. So as the simulation runs, each point process is observed using the tools such as the 10-second test, the 15-minute observation, the kaizen target report and kaizen event forms, and VSM maps. There are enough materials between both kits to run the simulation building cars continuously for as long as the team requires to stabilize the flow and prove the observations and recommendations.
Every 10 minutes or so the flow is stopped (frozen), results observed are discussed in terms of the customer, the team, inventory build up at process points, and the company. Improvement ideas are generated and implemented and the flow started up again. Metric charts are kept throughout the event and bottom line financial calculations record the progress as the team learns to transform the flow into a customer demand driven, resilient and responsive production process.
This event is intended to take a full day, or maybe two if the tools of improvement themselves are thoroughly explored. Each step requires at least 30 minutes minimum to run the exercise, collect data, hold a kaizen, implement improvement, and then run again. Much of the time is taken up learning to use the lean principles and tools of continuous improvement.
Throughout the events, the 60-page color printed facilitator guide provides lists of things to observe and point out to the people, comments to add for clarity, and suggestions for improvements to help keep the events on track.
The VSM Loop simulates the functions of supplier; stockroom; sub-assembly; final assembly; optional detail process; quality inspection; finished goods inspection; shipping; customer; material lugger; planning; purchasing and accounting. Each of these point processes or functional job elements can be the focus of the loop to explore ramifications of various process and procedures on the value stream and flow velocity. For example, assigning dollar values to components and labor elements allows the accounting function to tally cost metrics for warehouse and buffer inventories, cost impact of rework and stock-outs, and other hidden factory costs in each of the nine simulated flows.
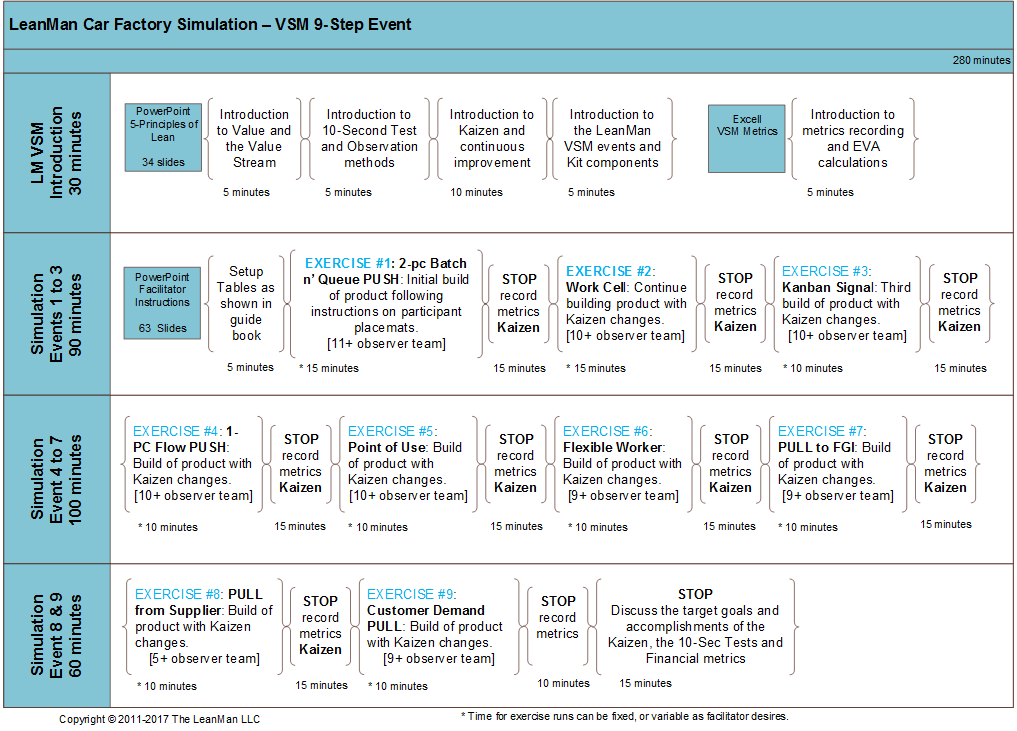
NUMBER OF PARTICIPANTS
The team set up is variable but works best with at least 12 people, typically 6 hands-on participants, 4 or 5 conveyance material movers, and 1 or 2 observers for the 10-Second Test and 15-Minute observation. The event is flexible and can be adjusted to accommodate between 10 and 15 participants with short notice, plus the optional Head Lamp/Tail Lamp Detail process can easily be added at the last minute. Table arrangement and role placement in relation to the Car Factory material kits is shown pictorially in the facilitators guide book. The facilitator tools include a printed and bound color guide book and PowerPoint presentation which provides a complete discussion of the VSM flow methods and metrics.
EVENT TIME
A single facilitator can easily control the team when using the printed and laminated participant instruction placemats provided as part of the kit. The Facilitator guide lists things to observe and point out to the people, comments to add for clarity, and suggestions for improvement. Please Note: after the first simulation run, the placemats become less necessary and as process steps are eliminated flow is determined naturally.
Event time is approximately 2 hours for the slideshow presentations on Lean and 2 1/2 hours for the simulation, although the event can run as a continuous loop for as long as desired. Allow plenty of additional time to experiment with alternate flows and to fully explore the lean tools and forms. Room size should be a large conference room or training center and should have at least five tables and space for at least 15 people. Separating the "departments" at different tables greatly adds to the realness of the simulation and conveyance people will move material between the department functions. Multiple rooms may be one option, with supplier and customer remotely located and required to use cell phones to communicate requirements to add some realism and fun.
LeanMan Grand Car Factory Simulation
$2,044.90
The LeanMan Grand Simulation Package is a reduced cost bundle of the Deluxe Car Factory Simulation, the VSM, the Kanban and the Heijunka events packaged into two double-deep containers. Now on SALE! Save $200.00