4-Step Kanban Simulation. (Random Customer-Pull Value Stream with Heijunka Sequencing)
This presentation event is part of the Deluxe-Plus Kanban Training Package, or the Kanban Upgrade Kit can be obtained as an optional purchase for use with the standard Deluxe Car Factory Kit or any of the other Deluxe-Plus Car Factory Kits. It is included in the Grand Package.
This Customer Demand-Pull event explores the flow control differences between a single kanban card and dual kanban card replenishment system with random demand. The LM Kanban Simulation is a complete value stream simulation with a focus on various kanban methods to control flow and inventory levels.
THE EVENT
The event is the Zoom-Zoom Car Factory and Showroom. Customers take delivery from the Show Room at random, which triggers stock replacement from the factory Warehouse, which then triggers the Planning Dept to order a replenishment from the Factory, which in turn causes a duplicate car to flow back into the Show Room. Along the way, various kanban methods are employed.
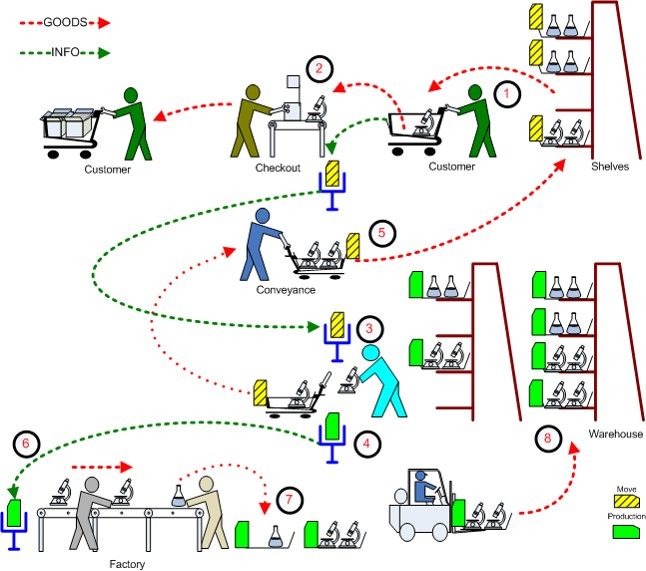
- A customer picks up the goods he wants from the shelf.
- At the checkout, the move card is collected into a kanban post (a collection box)
- Move cards are sent to the warehouse. As goods are picked, the move card is exchanged with the production card that was attached to the goods.
- As the exchange takes place, production cards are collected into another kanban post.
- The goods are retrieved from the warehouse and delivered to the supermarket shelves with the move cards attached.
- Production cards are brought back to the factory, where operators will manufacture only the amount indicated by the production cards.
- When production is completed, production cards are attached to the goods.
- Goods are then transferred to the warehouse.
The key to performing the LM Kanban Simulation is to allow the participants the time to fully explore the flow method and discuss in detail the ramifications of the lean elements presented, such as material flow to supply each area; or the difference between the factory push versus the heijunka sequencing.
- The first event explores a single kanban card replenishment system which is triggered by a customer pull from the Show Room. The event takes a look at how this single card causes action and reaction throughout the value stream, and how additional controls such as kanban signal flags and kanban material cards control inventory levels.
- The second event explores the dual kanban card system using MOVE and PRODUCTION cards, and shows the refinement of communication and flow they provide to the value stream. The additional of a kanban square improves control of buffer inventory levels.
- The third event explores the opportunities of further refining the inventory levels and flow internal to the factory using the lean principles. Supporting kanban methods are used to signal the Supplier release of materials to the Stock Room, where they are used to replenish a point of use inventory supermarket at Assembly. Kanban signal flags are used to control Conveyance to move materials, products and orders throughout the value stream.
- Finally, the fourth event explores the refinement of TAKT time and sequence control using Heijunka methods and queuing logic. Inventory and EV are improved with the reduction of buffer stocks to minimum levels and by driving Finished Goods inventory to near-zero while maintaining customer TAKT and on-time delivery metrics.
Little's Law is discussed and opportunities for calculating throughput rate, cycle time and wip provide some interesting discussion topics. Throughout each event Observers look for waste using the LM 10-Second Test method and general observation points as indicated in the facilitator guide. After each event the team is invited to hear the observations, perform inventory calculations using the Excel INV metric chart, and to calculate Earned-Value and Margin using the Excel EV chart.
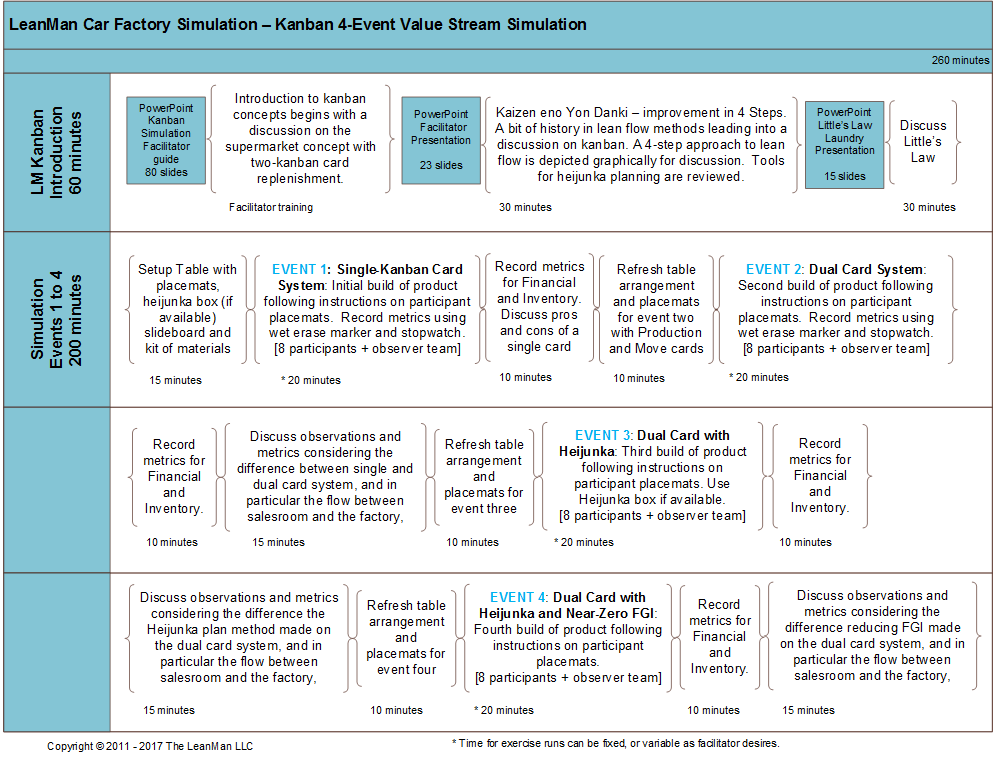
NUMBER OF PARTICIPANTS
The event set up is variable but works best when the Factory and the Show Room are separated by some space such that a Conveyance person is required. The Warehouse can also be separated from the Factory if there is adequate space available. The minimum number of participants is 7, then Conveyance people, Observers, and Metrics people can be added as needed.
FACILITATION
A single facilitator can easily control the team when using the printed and laminated participant place mat instruction sheets. The laminated sheets include heijunka calculator charts and wet erase markers, plus the Excel 10-Second Test, the Earned Value and Margin Calculator, and the Inventory metric calculators aid in keeping track of bottom line improvements.
EVENT TIME
Event time is approximately 1 hour for PowerPoint presentations and 200 minutes for the 4 event steps, but depends upon the facilitator and how much time is spent on focusing on specific opportunities such as inventory control, or kanban techniques, or financial metrics for each flow type.
LeanMan Grand Car Factory Simulation
$2,044.90
The LeanMan Grand Simulation Package is a reduced cost bundle of the Deluxe Car Factory Simulation, the VSM, the Kanban and the Heijunka events packaged into two double-deep containers. Now on SALE! Save $200.00