The Ultimate Simulation explores the concepts of the learning curve when introducing product into a production team, the techniques used to capitalize on the voice of the people include using kaizen methods, the 10-second test and the 15-minute observation teams to voice the obstacles in the flow, and to continually improve production methods with the goal of improving flow velocity. The Simulation begins with Batch Flow + Kaizen, then introduces 5-S methods, and based upon kaizen outcomes, implements 5-S, to finally develop a Lean Flow. Earned value analysis shows the way. The experience uses two identical Excavator products with over 200 components in a 5 work-station flow plus finished goods. The simulation can be presented in either 2 Half-Day events, or 1 eight hour Full-Day event.
Please Note: The game comes standard with the Excavator
Also, the game may be used with any of the Meccano STEM sets and extra may be purchased on Amazon, eBay or Walmart as available to expand the game and add participants. The Roadster is the most available as of 2025 on eBay or Amazon. Instructions for each are included in this package.
The following additional models, if available, may be added to your excavator order to provide additional participants to your event:
- Race car model 18207 - 1 unit in stock at the LeanMan. Contact Sales@TheLeanMan.com to add it to your order. Cost is $40.00 each.
- Excavator model 18208 - standard unit in this kit.
- Roadster model 18202 - 4 units in stock at the LeanMan. Contact Sales@TheLeanMan.com to add it to your order. Cost is $25.00 each.
- John Deere 8R 18302 - available at many toy stores.
NOTE: The LeanMan LLC no longer produces the OPT simulation, but now includes all of the material lists, PowerPoint and Word instructions, and materials you will need to obtain and perform this fantastic simulation on your own.
INFORMATION ONLY should you choose to purchase the OPT materials and perform the game.
The OPT Factory Simulation Dice Game explores the variables that influence production outcomes. OPT stands for Optimized Production Technology. A great introduction tool for new production supervisors, managers, and product planners, or anyone working in a production environment. You will explore all of the variables that influence production outcomes including material push, bottlenecks, line imbalance, batch sizing, 1 piece flow, pull, and more. This 8-hour course is also an excellent teaching tool for industrial training course work. There are 14 scenarios presented in either 2 Half-Day events, or 1 eight hour Full-Day event. The game can be played with 8 to 12 participants. Three additional participants can be added with extra chips and dice. Based upon a game inspired by Eliyahu Goldratt.
This is the underlying reason for the Ultimate Simulation with a mechanical product.
Many customers who own one of the LeanMan Car Factory Kits, using the wood cars and just a few components, have stated that those kits do a great job of displaying the principles of lean. However, having only a few components leaves little to discuss in the kaizen events when it comes to displaying the effects of communication, team interplay, the learning curve on the team. Such things like adding a new member to a well established flow will slow the flow until the new member learns the hands-on details and complexity of the process, how to perform it at speed, and how the communication system within the team works. While this simulation works well for most, some customers wanted a more technical training tool. They asked for a more detailed product to build with more variations and components.
Those customers have asked for a more technical process such that students in technical course work such as product engineering can study various process methods for assembly, with a goal of ever increasing efficiency in the process sequence. The Ultimate simulation provides a suggested sequence for the typical training session, but also includes a file with each step provided in a graphic such that the steps can be cut 'n pasted into a new instruction sheet and sequenced in any number of ways, thus the flow velocity can be analyzed for the best process. This simulation is an excellent teaching tool for the technical classes, but it is also a remarkable simulation as is for production people to just want to learn lean flow.
Thus, the Ultimate Simulation with the Meccano STEM units to build with over 200 components and some tricky assembly techniques. Thus, the learning curve from the 1st build in Batch Flow until the 4th build in Lean Flow is tremendous. The 1st unit in Batch typically requires over 90 minutes, while the 4th build in Lean has been performed in under 22 minutes. The changes to techniques required to improve flow along the way are very creative, and the kaizen events just flow with ideas on how to perform the tasks better. Everyone learns at a faster rate by sharing the "voice of the people."
The package also includes presentations on communication, both visual and aural, and team development and interaction, with a couple ice-breaker games that are fun to play and allow the team participants to get to know each other. One game involves tossing a nerf ball between members in a circle, and once at top speed, suddenly add or remove a member and watch what happens to velocity. Just like a person showing up late or not at all. A soft nerf-like ball is included in the package.
The Meccano STEM 18208 Excavator is available from various sources on-line, at eBay, and at Walmart and other toy sources. Additional sets might be purchased to create a parallel team for some fun competition, and to share insights during a combined Kaizen Event.
The Meccano models used with the Ultimate simulation can be purchased on the internet, at eBay, at Amazon and other toy stores. Additional sets can be purchased to expand training to multiple teams competing in parallel and sharing their kaizen experiences.
There are three models available and instructions for each are provided with the Ultimate package.
- Race car model 18207
- Excavator model 18208
- Roadster model 18202
- John Deere 8R model 18302
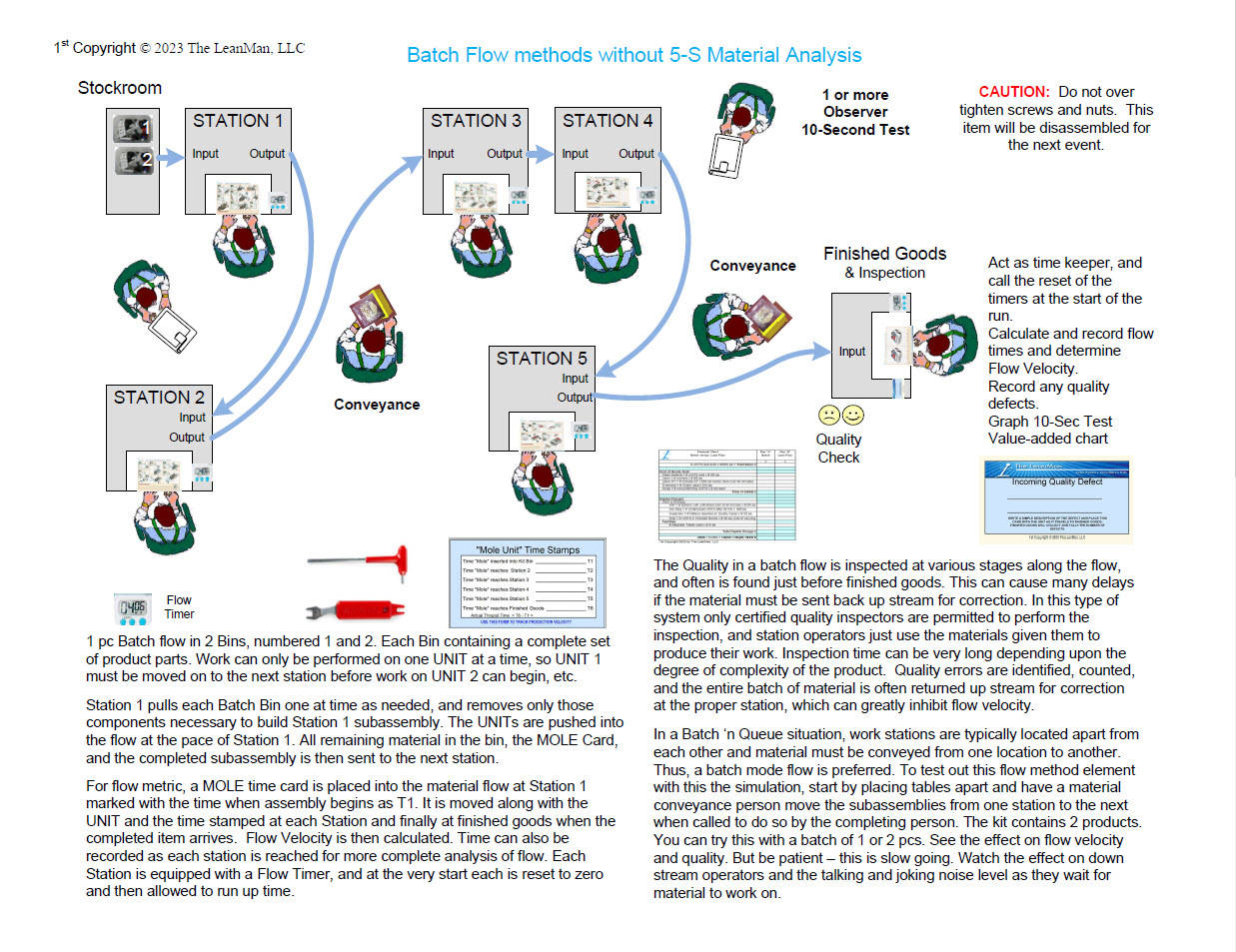
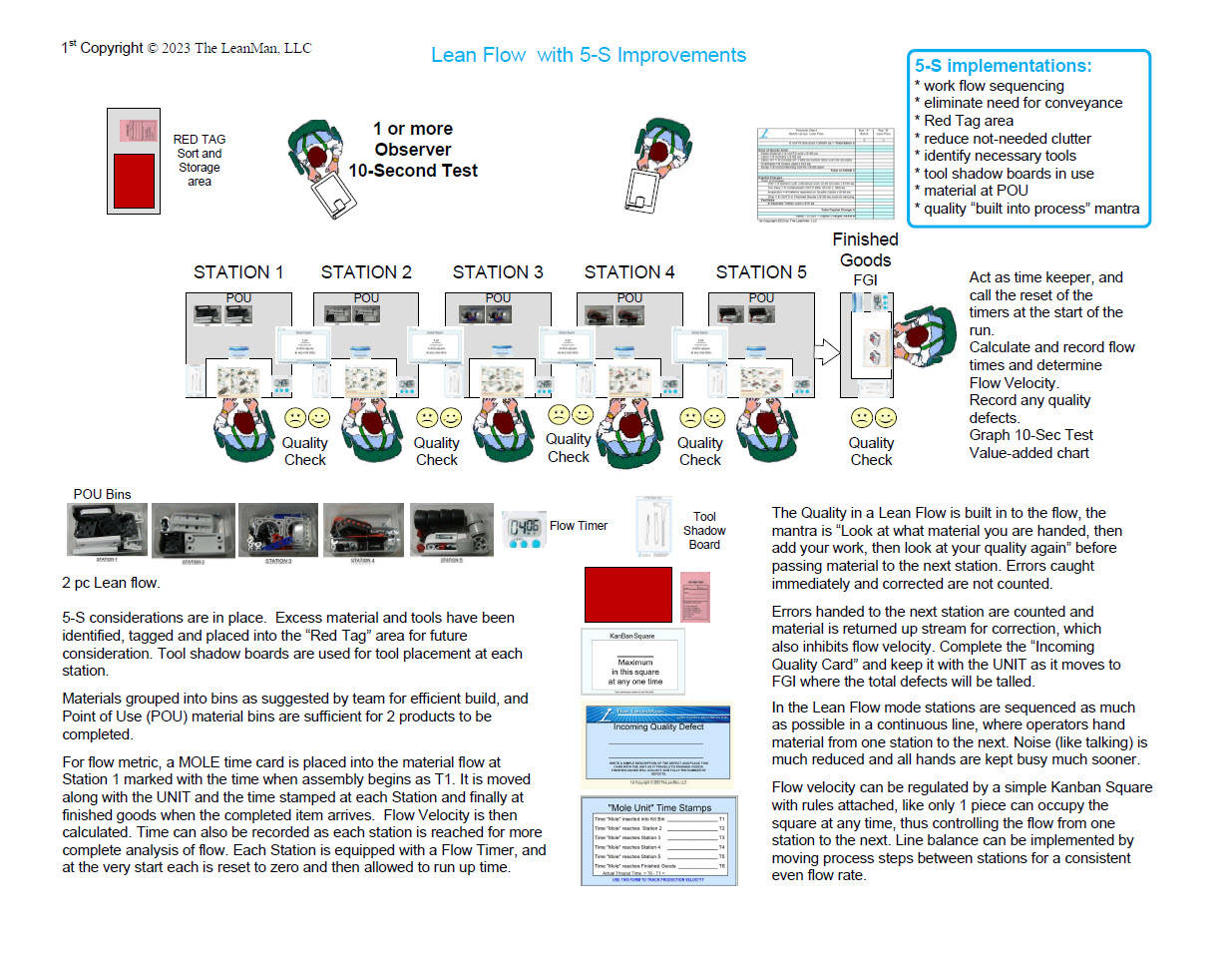
The student will come away with an understanding of the influence each variable has on production flow, learn about some tools that help to see the obstacles that stand in the way of flow velocity, the impact on the hidden cost of the factory on earned value and how to make the customer happy.
- Just how does the learning curve we all experience when starting a new task help with the next time we perform that same task, and how can we use that to our advantage in a process environment
- How does the voice of the people, or kaizen event, help to improve the flow velocity in a process stream.
- How does the kaizen event help to implement 5-S in the work place, and why is a clean and organized work place help improve flow velocity.
- How does simplifying the work stages help reduce quality errors and improve flow.
- What are the tools of 5-S that we can implement, and some practical methods of implementing 5-S.
- What is the hidden cost of the factory and how does that affect the earned value, or profit, of a company.
- What makes the customer happy? High Quality, On-Time Delivery and Lowest cost. How do each of these customer requirements help us to drive to perfection in a process stream and how do they play a role in a lean flow.
- How does the Earned Value financial chart help us to make good decisions about any changes we might want to make at a specific point process, and why are some changes better for the overall flow velocity while other changes may only improve a single point process to the detriment of the whole.
Before we begin, let’s discuss what any job means regardless of where we work.
A job is performing some work in a daily manner that is considered repetitive. You perform a series of tasks or steps to do something. It can be in an office typing letters and filing reports, or it can be in a hospital checking in patients and setting schedules, or it can be in a factory assembling objects into something a customer is willing to purchase. In all instances, the act of performing these tasks comes down to setting the task steps into a standard procedure, or what we call a written process or a standard practice, that can be followed each day by anyone to assure the same high quality results, every time, and thus make both our boss and the customer happy. In the office, the boss is happy when letters and reports are correct and done quickly. In the hospital, the patient is happy when the wait time is low and the results are good, and in the factory the customer is happy when the item purchased is of high quality and delivered on time.
In our factory, we will strive to make the customer happy. And that means a high quality product delivered on time and with low cost. To do this we must consider how to achieve these 3 goals: quality, on-time delivery, and low cost.
Let’s take an example the process of assembling a TV stand you purchased on Amazon.
It comes in a big box and weighs about 90 lbs. 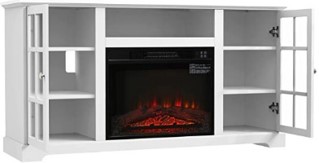
Since you are new to this process, you take the components out of the box, removing the Styrofoam packing and paper and cardboard and bags of “things.”
With the items, both large, heavy, and small, laying about you in disarray, you look at the process instructions and begin to try and sort out similar types, and dump out the bag of screws and pegs and included tools. You place everything around a central area where you will build the TV stand, probably on the floor since the thing is 90 lbs.
First step – get part A and B and it says “assemble together with the Philips screws S1.” You see that only an allen wrench is included in the “things” and so you need to go find a screwdriver. You continue to hunt down the proper items and assemble them using the allen wrench and screwdriver when instructed. It is tedious and the tools are small and take a lot of effort, and the screw location is usually in a tight location so that your hand is in the way. By the time you are finished your hand and wrist and back are all sore, and its now two hours later. And the thing is a bit wobbly.
But, it looks really nice!
Your friend sees the TV stand and says, wow, can you build one for me? You say sure. But this time you have learned a few things. When you lay out the components, you do so in the sequence you know you will need them.
You also know the heavy base can be set up on a couple saw horses at a height easy to work with no back pain. You know the assembly is held together with wood dowels, and if you glue the dowels, it will make the finished TV stand tight and eliminate the wobble. This time you are able to complete the TV stand in only one hour and it stands firm. Your back feels fine, but your wrist and hands still smart a bit from those small tools.
Now your daughter wants one for her apartment. You say, OK, but you are going to want to get better tools. You bring the saw horses and a hand-held drill driver with a Phillips bit and extension for the bit to give you plenty of operating room in tight corners. You lay out the components in the order you now know works well, and lay out the screws, dowels and brackets into separate piles for easy identification. The drill works great, the glue holds tight and the TV stand is complete in under 40 minutes. And you feel no pain!
There is a great deal of satisfaction in performing a job where we have a voice in the process to make something of value others appreciate.
To sum up: Every process has a learning curve. Every time we perform the process we learn how to improve it. This is what we call “continuous improvement” and factories use this technique in what we call a Kaizen Event, or the voice of the people, to improve a process. We will discuss what works and what doesn’t and how we might improve it.
Every Kaizen Event starts with the question, “What will make our customer happier?” The discussion takes off from that starting point, asking key questions such as:
- What is our quality rating?
- What is our flow velocity?
- What obstacles are still in the way?
Once we are satisfied that the process works well, we “standardize” the process in writing so that everyone coming after us can get the same good results. The resultant standard process produces better quality, a faster flow time and thus lower cost, plus more predictable on-time delivery. Or simply put we have a “happy customer! ”
And, as always, our overall goal in creating an efficient factory, other than making a profit, is always to make our customer happy !
The LeanMan suggests using the LeanMan Ultimate Simulation Package with 5-S in the following simulations:
Ultimate Factory Simulation
This full day event focuses on preparing the overall factory. Topics include Batch Flow, Kaizen Events, 5-S Implementation, and Lean Flow. Focus in on Earned Value and how to make the customer happy
.
- Group Size: 8-12
- Duration: 7+ hours
- Steps: 4